When doing quality inspections, it’s nearly impossible to test all products of a batch as it is very time-consuming and expensive – which will in the end completely eat up your margin. But of course you want to ensure your products are of high quality.
So how can you assure the best quality with as little effort as possible?
The solution: AQL sampling!
This blog post is for everybody who is looking for a way to decide whether to accept or reject an order during quality inspection in a less costly and still reliable way.
Find out everything you need to know about AQL sampling here!
- What Is Acceptable Quality Level (AQL)?
- Acceptable Quality Level Formula: How Is the AQL Calculated?
- 5 Factors that Should Influence Your AQL
- What Is an Acceptable Quality Level that You Should Aim For?
- How to Use AQL Sampling Charts - Step-By-Step Explained
- Conclusion on AQL: A Helpful Standard For Quality Inspections
What Is Acceptable Quality Level (AQL)?
Acceptable Quality Level (AQL) is a quality standard that was published by the International Organization for Standardization to assess the statistical quality of products at quality inspections.
It is a method that describes the worst quality level that is tolerable for a product and defines whether or not an order has met the client’s specifications.
The AQL usually is a percentage which represents the maximum number of defective units beyond which a batch is rejected. During a quality inspection, goods in a sample are randomly tested by a quality inspection company.
If the number of defective items stays below the AQL percentage, that product is said to meet the AQL. Batches of products not meeting the AQL will typically be rejected. It is advised to review the production process to eliminate the defect.
Let’s say you are selling medical gloves with an AQL of 1 %. That means that no more than 1 % of the batch being tested can be defective in order for your products to meet the AQL. So if your batch consists of 500 products, only 5 products can be defective. If 6 or more products are defective, the whole batch will be rejected.
Acceptable Quality Level Formula: How Is the AQL Calculated?
In quality inspections, normally not all products of a batch will be tested. AQL charts determine how many random samples will be pulled out and tested by the product inspection company.
In order to use these tables, you need to know your products’ AQL. But: The AQL is not a number that you need to know or that is always the same – it’s up to you to choose one for your product!
Important NoteThere Is No AQL Formula!
You need to choose the AQL. There are a few factors you should take into consideration when doing so.
5 Factors that Should Influence Your AQL
So when you are choosing an AQL for your products, keep the following factors in mind:
- Which Market Are You Selling To – Every market has its own standards for the AQL. Find out what the common AQL is in the market you are planning to sell to and adapt to it accordingly.
- Which Risk Is Associated With Your Product – The AQL also depends on the type of your product. Generally, the higher the users’ risk is, the lower the accepted defect rate will be. So if a defective part might cause severe injuries or even death, then the AQL is 0. That is why for pharmaceuticals or plane parts for example you will rarely find a rate that is way lower than 1%.
- How Much Effort Is Spent to Develop Your Product – Companies who spend a high amount of money in the development of new products are able to aim for lower levels because they can expect to face less defective products.
- Have You Worked With Your Supplier Before – If you have worked with your supplier before and already have a feeling for their work’s quality, you may be able to set a lower level as well.
- How Much Is Your Budget – Finally, the higher the AQL, the higher the cost for your quality inspection will be. So keep that in mind too – but don’t forget that defective products may cost you even more.
What Is an Acceptable Quality Level that You Should Aim For? 3 Types of Defects
There is no definite answer what a good AQL is. As mentioned before, there are a few factors that influence the AQL and therefore it differs from product to product.
Generally, you can also set up different AQL depending on the type of defect:
- Critical Defects – Defects that could potentially harm users and therefore are unacceptable.
- Major Defects – Defects that are usually not acceptable by the end-users as they are likely to result in failure.
- Minor Defects – Defects will probably not reduce the usability of the product which is why end-users would not mind them but the products differ from the specifications.
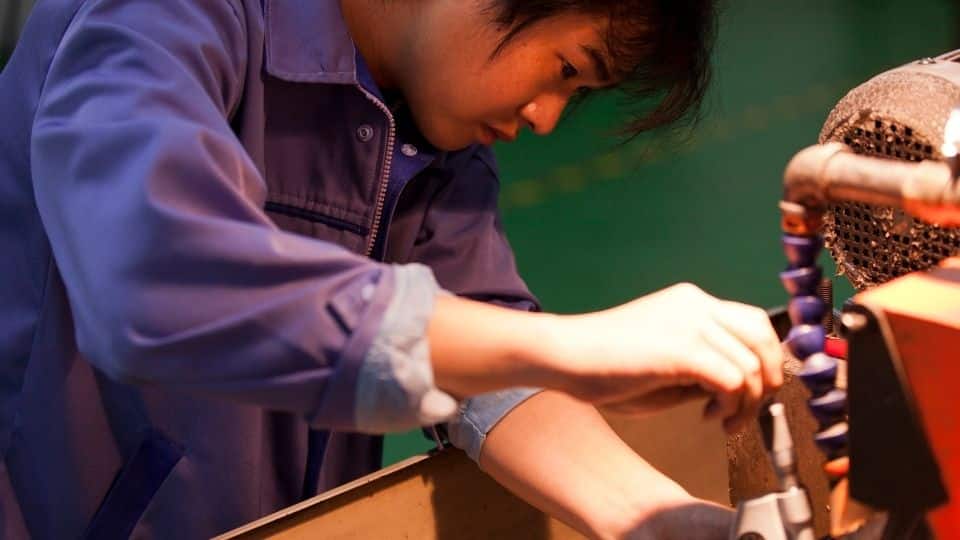
The average AQL span goes from 0 to 6.5 %.
What are the most commonly used AQL for consumer products in North America and Europe? Let’s have a closer look on some AQL examples:
- 0 % for critical defects
- 2.5 % for major defects
- 4.0 % for minor defects
How to Use AQL Sampling Charts – Step-By-Step Explained
So know that you know how to choose the AQL, we can get back to the AQL charts which are used to determine
- how many samples from a batch should be picked and inspected and
- where the line is drawn between acceptable and unacceptable defective products.
While you will find AQL calculators online which will provide you with all the numbers you need, it definitely makes sense to understand the concept behind these calculators to be able to interpret the numbers properly.
So let’s go back to our example with the gloves: You have ordered 500 of them all produced in a single batch. You have agreed on an AQL of 1 % for all defects.
1. Find the Right Row According to Your Lot Size
In the first step, you need the following chart (table 1). Find the row that corresponds to the size of your batch.
In our example, you ordered 500 products.
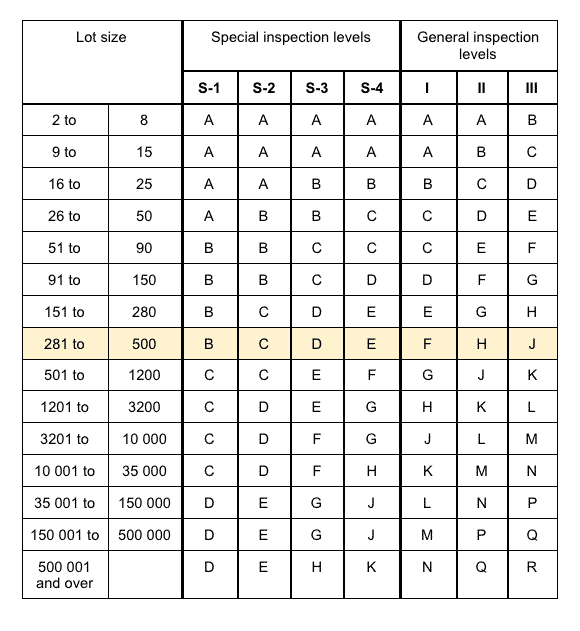
2. Determine the Inspection Level
Next, you want to determine the inspection level. There are three General inspection levels.
- Level I – If you are only inspecting fewer units, level one can be used to reduce the costs as it takes less time – but on the other hand, the results will not be very reliable. They will only give you a first impression.
- Level II – In most cases, inspection level II is used. It’s the good medium ratio between input and results.
- Level III – If you are working with a new manufacturer that you don’t trust yet because of the lack of experience in working with them, it makes sense to opt for additional units and choose level III.
PRO TIPPick the Standard Level II for Your Quality Inspection!
The higher the inspection level, the more reliable the results! Level II Is used in most cases.
The Special inspection levels play a role when you want to run specific types of tests. They are usually not used for the entire inspection.
In our example, we will go with Inspection Level II.
3. Find the Sample Size Code Letter
Next, find the sample size letter by looking for the part where both rows (the Lot size and the General Inspection Levels) cross.
In our example, the Sample size code letter is “H”.
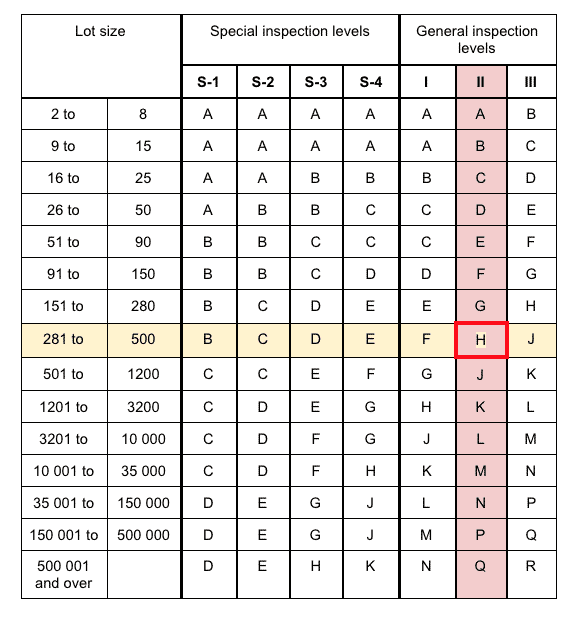
4. Find Out the Sample Size
Now you need a second chart (Table 2-A). Look for your Sample size code letter. On the right side next to it, it will give you the sample size.
For the letter H it shows you need a sample size of 50. That means in your quality inspection, at least 50 units should be pulled from the batch.
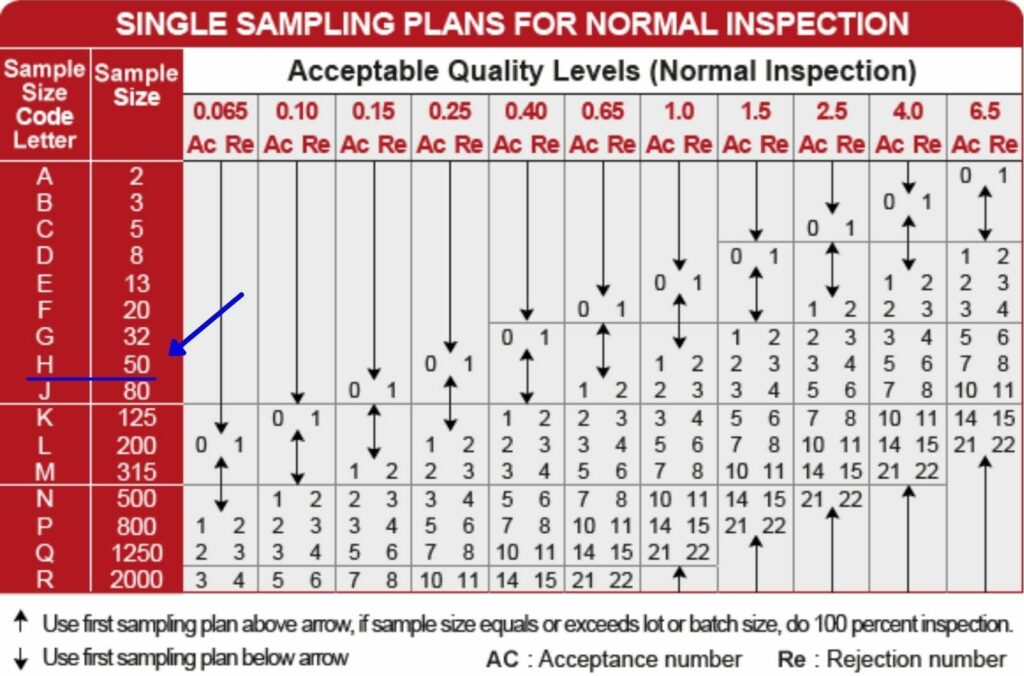
Source: QIMA
5. Determine the Number of Allowable Defects
To determine the number of allowable defects, follow the row and look for the intersection with the appropriate AQL column.
In our example, we chose an AQL of 1. In the row of our Sample size code letter it shows the numbers 1 and 2.
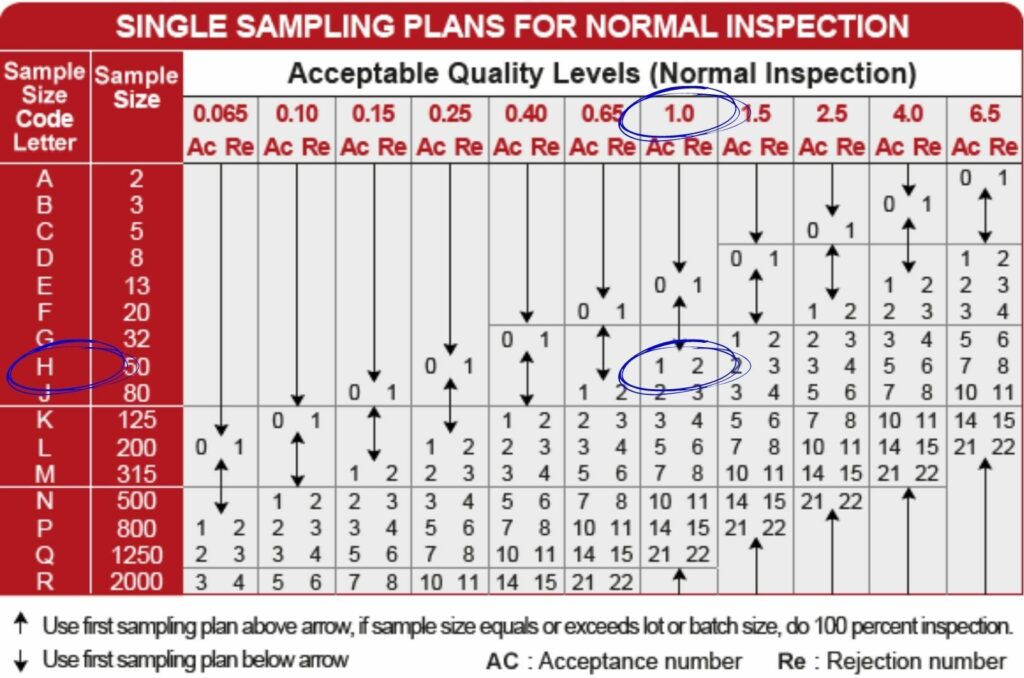
Source: QIMA
So what does that mean?
The lower number, 1, stands for the maximum number of allowable defects that will result in acceptance. The higher number stands for the number of defects that will result in rejection.
So for our example with an AQL of 1 % that means
- If 1 or less defects are found, the batch will be accepted.
- If 2 or more defects are found, the entire batch will be rejected.
Conclusion on Acceptable Quality Levels: A Cost-Efficient Method for the Best Quality
As you can see, AQL sampling with AQL tables comes in very handy when you want to ensure high quality during a quality inspection without having to test every single product of a batch.
Of course AQL sampling doesn’t mean your batch will come with zero defects, however you will get the best results for a reasonable price.
The process might seem a bit confusing at first but if you read this blog post carefully you should be best prepared for your next quality inspection.